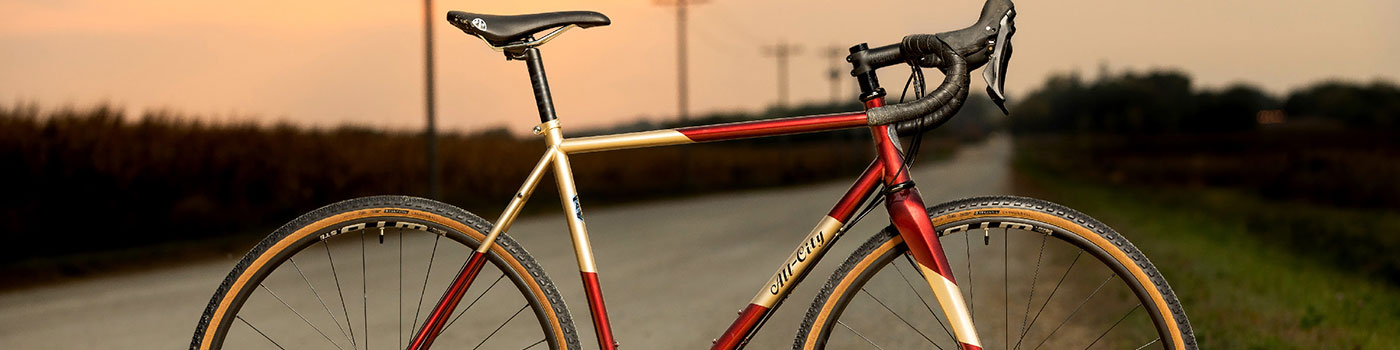
Tubing: A.C.E. Steel
ALL-CITY A.C.E. STEEL: HIDDEN STRENGTH
A - Air-hardened
C - Custom
E - Extruded
Here at All-City, we talk about bringing beauty back to production bicycles whenever we get the chance. We give a damn about honoring our industry’s history and we’re stoked to have a hand in shaping its future. One way we’re doing that is by exploring the incredible potential of steel.
Steel got its start in the bike industry back in the 1880s, and some of today’s riders might think the material peaked with disco. You might overlook it, too, if you knew those late 19th-century models weighed upwards of 80 pounds. But today’s strong and lightweight frames aren’t made solely from aluminum, carbon, and titanium. We believe high-quality steel tubes still have a place at the podium, on the pavement, and in all the wild places in between. And we’re out to prove it.
First introduced in 2016, A.C.E. steel is our proprietary air-hardened, custom-extruded steel tubing. Unlike off-the-shelf tubes readily available from suppliers, A.C.E. allows us to cut unnecessary weight and pursue the thinnest walls possible without sacrificing strength. It’s given our engineers the freedom to go completely custom with butting profiles and wall diameters on a number of bikes in our line. From the Zig Zag to the Nature Cross to the Cosmic Stallion, each unique A.C.E. tubeset is fine-tuned for absorbing bumps and doing the specific job it’s been asked to do.
But why did we develop it? And how did we get here? And where are we all going next? If you’re into it, let's take a ride.
WHY WE DEVELOPED OUR OWN STEEL TUBESET
In years past, we’ve designed and built bikes from some spectacular name-brand steel tubes — Columbus Zona and Reynolds 853, namely. We’ve also built excellent bikes from solid off-the-shelf materials where appropriate. (Check out our 612 Select offerings some time.) But unlike straight-gauge tubes with a consistent wall thickness from end to end, the strong and lightweight Zona and 853 offerings feature aggressive butting profiles — thin in the middle of the tube and thicker at the joints and other high-stress areas where extra strength is needed. Working with these materials helped us realize the potential for lightweight steel bikes and lit a fire under us to pursue it.
LET’S TALK ABOUT FOOD FOR A MINUTE
We briefly touched on what makes A.C.E. special above — the freedom it affords our engineers to explore the exciting balance between strength and weight — but aren’t they free to select tubes from any supplier they want? It’s a valid point, so here’s another way to look at it: Let’s say you’re making a big lasagna for dinner. First you find a recipe over at NYT Cooking, then you zip over to the grocery store to pick up the ingredients. You make dinner, everyone eats, success! That was a very nice pan of off-the-shelf pasta.
But let’s say instead you want to make a lasagna unlike anything you’ve tasted before, and you want complete control over what goes in it. Are you going back to the grocery store, or do you want to use the tomatoes and herbs from your own garden? And what about the cheese monger at the Farmer’s Market? She knows what’s up. Her fresh mozzarella has exactly the acidity you’re after. And so you do this dance with every ingredient you can, going deep on how each was made and handled so you can be sure you’re putting together the exact meal, or bike, you’ve been dreaming about. Maybe you’re not milking the cow or welding the tubes with your own two hands, but you’re also more involved in the process than a customer pushing their cart toward the self-checkout lane. You’re a partner in production.
WHAT MAKES A.C.E. STEEL SO DELICIOUS
If you’re wondering what this means in terms of our steel tubes, let’s look again at what A.C.E. stands for: Air-hardened, Custom, Extruded. Steel is made stronger and more resistant to damage when it’s repeatedly heated and cooled. This process involves cycling between very precise, very extreme temperatures. You can dip the metal in a water or oil bath to cool it rapidly, or you can blow inert gases over the steel to lower its temp at a slower, more controlled rate. Both methods can produce fantastic results, but we prefer air-hardening for our bikes because rapid cooling will sometimes cause cracking.
Extrusion, on the other hand, refers to how the tubes themselves are formed and shaped. Tubes with welded seams are formed by rolling strips or sheets of steel into a tube shape and then welding the seam the long way down. This simple method produces affordable, readily available tubes with a long noticeable scar on the surface. Sick scars tell stories, sure, but you know we hang our hats on aesthetics around here. That’s one reason why we prefer the extrusion process. Kinda like pushing Play-Doh through fun shapes like stars and moons, A.C.E. tubes are drawn from a solid semi-finished chunk of steel — a billet — and then extruded into a hollow form. Along with looking clean as heck, seamless tubing offers superior strength and corrosion resistance. Pair these properties with air-hardening and you’ve got tough steel bones that don’t have to be heavy to be strong.
HEADACHES AND HIDDEN STRENGTH
Having full control over the development of A.C.E. steel tubes has provided undeniable benefits, both for our brand and the bikes we put out in the world. But the road to gettin’ here wasn’t always smooth, and success was never guaranteed.
Developing a new product takes time, first off. And when you’re working in the unknown — taking risks with unproven tube dimensions, for example — passing testing isn’t a given. When we received prototypes of our very first A.C.E. steel cross bikes, now called the Nature Cross, we were blown away by how lightweight they were. On some of the very first frames, we were even flirting with titanium-equivalent weights. Those frames didn’t pass testing in the end, so we had to beef ‘em up and try again to get it right. Iterations like these require a great deal of back and forth with our manufactures, sometimes significantly delaying or derailing a new bike.
But the failures make us better and can lead to creative solutions. Case in point, when we were developing and launching the Log Lady, our first A.C.E. steel bike, we knew we needed to make a strong joint where the downtube and headtube meet up. Instead of welding a bunch of extra material to the frame’s exterior to get the strength we needed, we accomplished that on the inside of the frame by making the bottom of the tube thicker than the top. Call it asymmetric butting, call it hidden strength — we didn’t see much of that happening outside the BMX world, and doing it this way allowed us to keep the frame’s silhouette looking clean.
Through frequent correspondence with our tubing vendor in Taiwan, All-City Design Engineer Jenny Carmichael has learned to anticipate potential problems before they pop up. “It’s tough to pass testing when you’ve got holes in the tubes [for internal cable routing],” she says. “But if you’ve controlled the butting profiles, it’s easier to get a successful test.”
Not every failure can be avoided, though. “We had a steel bike in development that we were trying to get under a certain weight target, so we tried decreasing the diameter of the downtube. We took a pound out of the bike that way. They took every suggestion I made, but then it failed testing with cracking. So now when they say no, I understand my suggestion may not work. And when they say yes, I can feel confident about my recommendation. ORA has a pretty good idea what will work and what won’t, and they don’t want to make bikes that fail.”
WHAT’S NEXT FOR A.C.E. STEEL?
We’ve talked a great deal about the time and effort required to develop lightweight, high-quality steel tubes. At this point, you may be asking yourself, “Why not ditch steel and make all the bikes out of aluminum or carbon? The answer: Steel’s smooth ride quality cannot be beat.
Steel truly excels on mixed terrain. Gravel and double-track are hotter than a Happy Meal right now, and our A.C.E. steel Cosmic Stallion eats it all up. “Everyone wants gravel and all-road,” says All-City Brand Manager Nate Choma. “So bike brands are looking at the problem and asking, ‘How do you ride long distances over this incessant bumpy terrain?’” Some are taking aluminum or carbon frames and adding light suspension all over the bike — under the seatpost, under the stem, all sorts of interesting places.
But if you look at steel, a material that’s been used on bikes for nearly a century and a half, it does everything you need it to do on rough terrain. It absorbs the bumps, it provides efficient power transfer, and it does so without those additional technical solutions. “Some of our steel bikes,” Nate says, “are head to head in terms of weight with carbon products because we don’t have to put anything on there for vibration damping or compliance. I love the route we’ve taken with steel; it’s a simple solution, and we’d be foolish to ever forget about it.”
As the all-road category becomes more mainstream, our investment in A.C.E. is only reaffirmed. Steel is not a dead material. It’s alive and kickin’ and just begging you for a ride.